About Us

On the market since 1948
Rustavi steel LLC
In 2011, Rustavi steel LLC was established to acquire the assets of the Rustavi Metallurgical Plant. Rustavi Metallurgical Plant one of Georgia’s largest industrial enterprises, is situated 30 kilometres to the south of Georgia’s capital Tbilisi. The Plant is the largest metallurgical complex in the entire Caucasus region.
The Rustavi Metallurgical Plant was founded in 1948 as the first fully integrated metallurgical complex in the South Caucasus and produced steel, hot-rolled seamless pipes and various products made of pig iron, aluminium or iron. The Plant produced seamless pipes to meet the requirements of the oil fields of Kazakhstan, Azerbaijan and Turkmenistan.
Today, the new management and owners of the Rustavi metallurgical plant aim to restore the plant and develop its activities in regional and new world markets as part of a major investment and restructuring program.
Today, the plant is successfully operating and produces many types of products, including fittings, stainless pipes, square products, iron castings, metal structures, mechanical parts, mould castings, granulated slag, silicomanganese, lime and limestone.
For the Rustavi metallurgical plant to strengthen its position in the market, the first task is to increase the production volume. For this purpose, the new management is consistently carrying out systematic renewal and technical retooling of the factory, and introduction of new technologies. One of the main priorities of the factory is the training of young staff with the support of experienced employees.
Today, the Rustavi metallurgical plant exports its products to the markets of the European Union, the USA, as well as neighbouring Armenia and Azerbaijan. Today, more than 1,600 people are employed in Rustavi Steel
Since January 2012, the Rustavi Metallurgical Plant has been under the management and ownership of "Rustavi Steel" LLC. The goal of "Rustavi Steel" LLC is to give new life to the proud and long tradition of steel production in the city of Rustavi, which dates back to 1948. The new management of Rustavi Metallurgical Plant has embarked on a course of extensive reconstruction and development to create a modern plant that produces high-quality products for our loyal customers, both in Georgia and abroad.
We renewed the production of large diameter seamless pipes from D to "400" and started exporting products to the markets of the CIS, EU member states and the United States of America. Seamless Rustavi steel pipes are used in machine building and other types of construction, as well as in oil and gas production. This plant has the capacity to produce 350,000 tons of large diameter pipes per year, although it needs to be modernized at this stage. In this direction, we already have concrete plans on how we will start implementing this plan.
We produce all sizes of fittings for the construction industry, which are sold in Georgia and also exported to neighboring countries. Many important projects, both infrastructural and development, are being built with Rustavi steel reinforcement. Our goal is to sell 12,000 square tons of fixtures and fittings every month by the end of the third quarter of 2018. As part of our interim plant plan, by the end of 2018 we plan to increase the capacity of the plant's existing steel mill to 200,000 tons per year.
Also, the factory repair workshops were re-worked, where mechanical, foundry, sortaglin, electrical repair and other auxiliary workshops are combined, which ensures meeting the internal needs of the factory and providing services to the customers of the factory.
Rustavi metallurgical plant has implemented and operates a quality management system, which was developed taking into account the requirements of international standards ISO 9001 and API Spec Q1. Compliance and effectiveness of the quality management system have been confirmed by authoritative international organizations. We have introduced modern production methods in the last two years, we are conducting quality control and we are improving it every day. "6 Sigma" methodology is also in the process of implementation. This is a known process that ensures quality.
As part of the long-term plan, we are planning to rehabilitate the Zhmed complex with the goal of producing 650,000 tons of cast iron per year. Zmmedi is a complex that will receive cast iron from the ore. In the past we had two wise men who stopped in the 90s. One of them was scrapped during the previous owners, and we still have one and it can be restored for a certain amount of money. The difficulty is that the necessary iron ore is in Azerbaijan. Therefore, in case of making investments, the Ministry of Economy helps us in providing ore. A profitable and long-term plan with Azerbaijan should be developed to develop the above-mentioned wisdom. The development of Zjmed will allow us to produce 650 thousand tons of cast iron, which is in total demand. Cast iron is a product like oil - the more you produce, the more you sell. Cast iron is in great demand in the world markets, especially in the Black Sea markets. After the seamless pipes, the opportunity to export tens of millions of dollars is created in this direction as well. If we fulfill these plans, we can safely say that the Rustavi metallurgical plant will return to its old level. In case of commissioning of Zmmedi complex, we will be able to load up to 50% of the factory. Also, with additional investments, it is planned to set up a new oxygen furnace, which will melt cast iron into steel. The production of these products, in turn, will create the basis for the production of other new products.
Our goal is to strengthen the Rustavi metallurgical plant as one of the leading industrial enterprises in the region and increase its reputation internationally. We intend to achieve this goal by producing the highest quality products and exceeding customer expectations in the process of service delivery. The positive feedback and strong support we receive from our customers further helps us achieve our goals. It is our desire to assure current and potential customers of Rustavi Steel of our complete and ongoing commitment to the cause.
History & Heritage
- In 1940, the government of the Soviet Union decided to build a metallurgical plant in the town of Rustavi. This decision was based upon the presence of raw materials in the region and upon the town’s close proximity to existing oil fields on the Caspian. Building works began, but were halted by the outbreak of the Second World War.
- On the 23rd of March 1944, building was resumed around the South Caucasian railway station of Rustavi.
- In 1946, the first auxiliary workshops (the power plant, the mechanical repair workshop, the shape-casting workshop, the metal construction workshop, etc.) began to operate.
- In 1948 the Plant was officially established.
- On the 27th of April 1950, the first 150 tonnes of open-hearth Georgian steel were smelted.
- In September 1952, the first hot-rolled seamless pipes were produced on the Plant’s tube-rolling workshop’s “Mill-140”
- In December 1953, the “Mill-400” of the Plant’s tube-rolling workshop was rebuilt; in those days, the mill was the largest of its kind in Europe for the production of seamless pipes.
- In July 1954 the first Georgian pig iron was smelted in the Plant’s blast furnace.
- In 1954, the first Georgian coke was produced.
- In 1955, the Plant’s sheet and re-bar workshops began to operate.
- In 1961, the Plant’s cold-drawing workshop began to operate.
- In 1962, the automation of the tube-rolling workshop’s “Mill-400” was completed.
- In 1967, the Plant’s continuous-casting machine produced its first cast slab.
- Between 1961 and 1991, the Plant’s main installations were systematically modernized, its capacity was increased and the quality of its production was improved
- Between 1975 and 1980, the Plant’s open-hearth furnaces were modernized and their capacity was increased from 150 to 200 tonnes.
- In 1980, following the reconstruction of the Plant’s blast furnace, its capacity was increased from 750 to 1,093m3.
- The Plant’s new sintering plant began to operate in 1982.
- Between 1944 and 1999, the Rustavi Metallurgical Plant produced around 50 million tonnes of steel and over 36 million tonnes of pipes, reinforcing bars, sheet metal, etc.
- In 1999, the Rustavi Metallurgical Plant ceased to operate.
- In 2006, a British-Georgian private company bought 100% of the Plant’s shares, and the difficult process of rehabilitating it began.
- In 2009, induction furnaces were installed in the Plant’s steel-melting workshop and the Plant’s modernized shape and bar production workshop resumed production of re-bars.
- In 2011, after an interval of several years, the Plant’s production process resumed. More specifically, different diameters of seamless pipes were produced on the tube-rolling workshop’s “Mill-400” following an order placed by a large international company.
- In 2011, the Plant’s owners and new management brought back its old, historic name. To recover its former importance and to strengthen its market position, the first task will be to increase the Plant’s production capacity. Management is currently implementing measures for the Plant’s systematic modernization and re-equipment, is introducing new technologies and is training young employees with the help of experienced professionals.

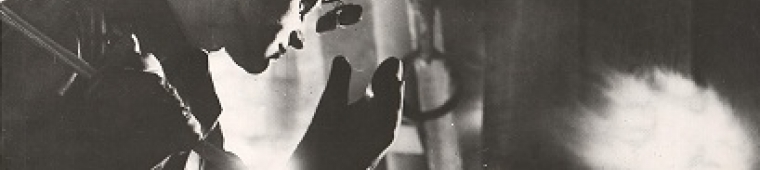
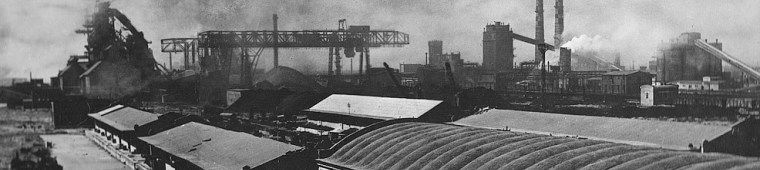
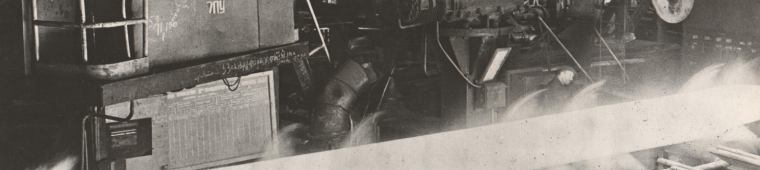
Corporate Vision
The main priority of the Rustavi Metallurgical Plant’s corporate vision is to strengthen the Plant’s position on both the local and international markets by producing high-quality products. In doing so, the Plant will contribute to the development of the country’s industrial sector.
Professionalism
High quality
Client orientation
Innovation
Health and safety and environmental protection
Teamwork
Facts & Figures
At the height of its production, the Rustavi Metallurgical Plant was producing the following every year:
- 620,000 tonnes of coke
- 1,200,000 tonnes of sinter
- 1,450,000 tonnes of steel
- 700,000 tonnes of pig iron
- 500,000 tonnes of seamless pipes
- 130,000 tonnes of sheet metal
- 130,000 tonnes of bolt stock
- 1,200,000 tonnes of pipe billets
The Plant’s capacity used to be the following:
- a sintering plant with a nominal annual production capacity of 2.2 million tonnes
- a blast furnace with a nominal annual production capacity of 725,000 tonnes
- two coke batteries with a nominal annual production capacity of 350,000 tonnes
- eight 200-tonne-capacity open-hearth furnaces with a nominal annual production capacity of 1.5 million tonnes
- a “Mill-1,000” blooming mill with a nominal annual production capacity of 1.5 million tonnes
- a “900/750” billet mill with a nominal annual production capacity of 1 million tonnes
- a “Mill-140” seamless pipe mill with a nominal annual production capacity of 120,000 tonnes
- a “Mill-400” seamless pipe mill with a nominal annual production capacity of 350,000 tonnes
- a workshop for cold-drawing pipes with a nominal annual production capacity of 50,000 tonnes
- a “Mill-320” reinforcing-bar mill with a nominal annual production capacity of 160,000 tonnes